Most attic areas are vented, meaning that the attic is designed for exterior air to flow through its space, ideally helping to keep the attic temperature and moisture levels moderated. Ambient temperature air flows in through the lower level vent openings, usually in the soffit area, passes through the attic area, and is drawn or forced out the upper level vent openings, usually at or close to the peak of the roof.
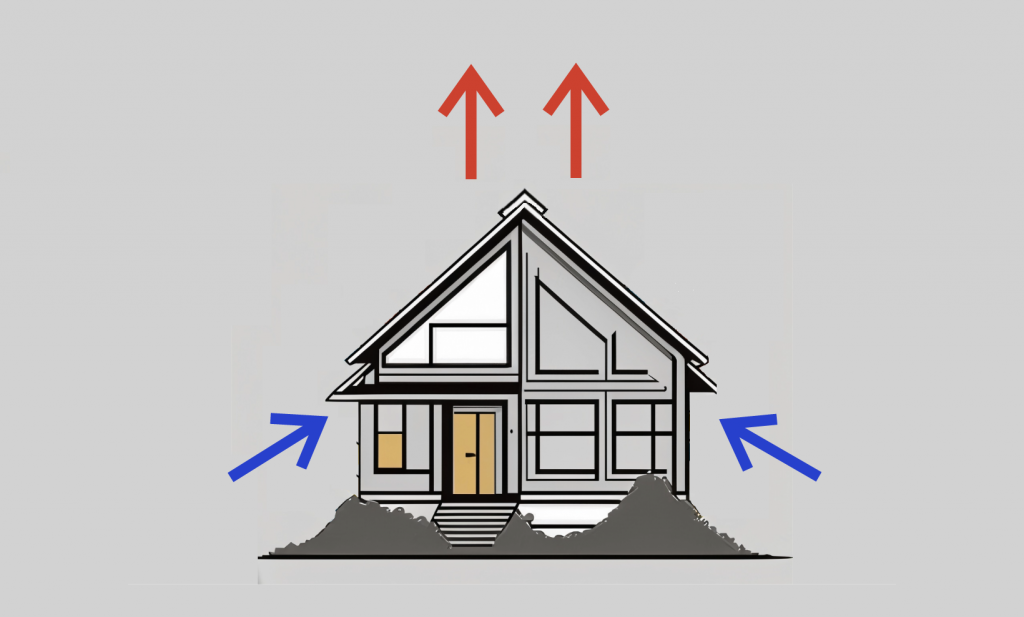
In contrast, unvented attic assemblies are formed when a layer of insulation is found at the roofline and natural ventilation is eliminated from the attic space. This results in the attic assembly becoming a part of the conditioned space of the home. (Some experts prefer to classify this type of attic as “semi-conditioned”.) This configuration is often utilized to improve the energy efficiency of a structure, increasing comfort levels and decreasing energy usage.
However, when a structure is converted from a vented to unvented attic, proper protocol must be followed. Problems may result from improper attempts at creating an unvented attic assembly.
There are many different (and often conflicting) guides, standards, codes, and instructions addressing this type of attic conversion, and fully inspecting for compliance with these various rules is beyond the scope of a standard property inspection. If you are purchasing a building with an unvented attic assembly, we always recommend having a trusted expert evaluate the assembly prior to the end of the inspection period, to verify proper construction.
Some of the guidelines required by the International Residential Code include:
- Given that changing to an unvented attic assembly may change the HVAC needs of the building, the HVAC system must be either properly sized or modified to the correct size
- Any insulation installed in the “floor” of the attic, above the living space, must be removed (with some exceptions for insulation installed under appliances in the attic)
- All outside ventilation to the attic area must be properly sealed (as the attic should now be unvented)
- Any Class I vapor retarders installed between the unvented attic and the living space (typically installed at the “floor” of the attic) must be removed
Special consideration must be given to any fuel-burning appliances located in the unvented attic space, as each appliance will need a source of combustion air for safe operation. Some units are specially designed for use in unvented attic spaces, while others require some additional installation steps to properly function in this type of environment.
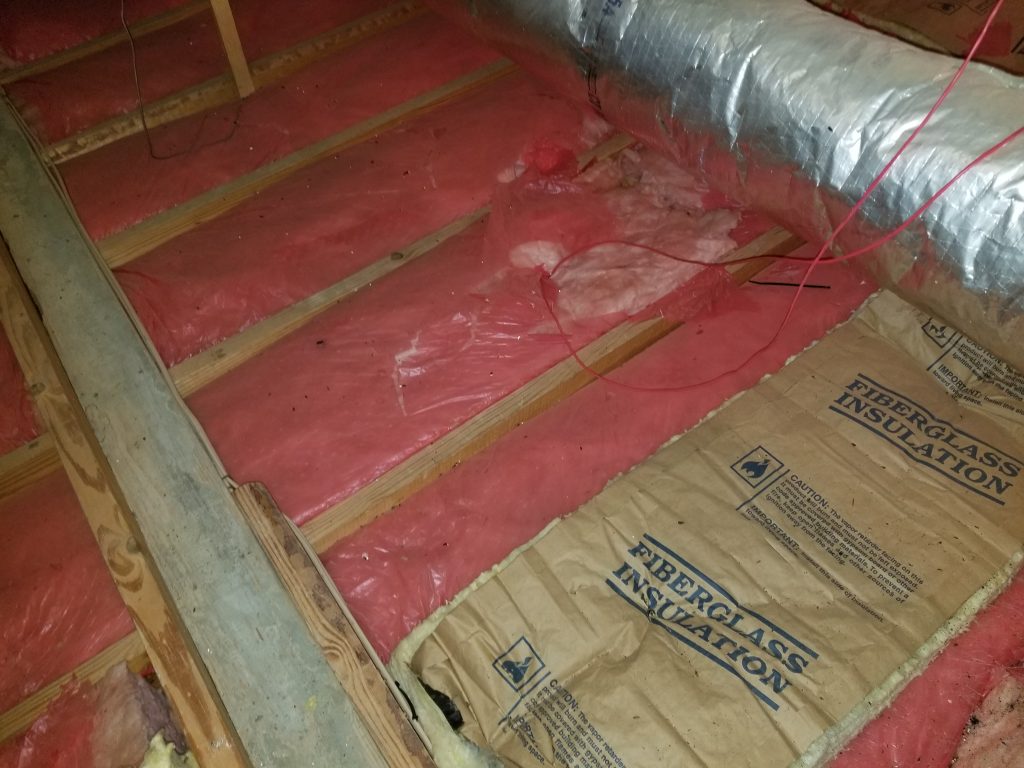
In climate zones 2 and 3 (which encompasses the state of Louisiana), additional requirements must be met:
- The roof pitch must be 3:12 or greater
- An approved vapor-diffusion port must be installed within 12″ of the highest peak of the roof
Please remember that fully inspecting unvented attic assemblies for compliance with all the various rules and standards is beyond the scope of a standard property inspection. If you are purchasing a building with an unvented attic assembly, we recommend having a trusted expert evaluate the assembly prior to the end of the inspection period, to verify proper construction.